A floating slab or “Alaskan slab” is a slab unit constructed over a pad of percolating material grade made of coarse sand, gravel, or crushed stone. The name “floating slab” means the slab is allowed to move above the frost line as a single unit as if it floats.
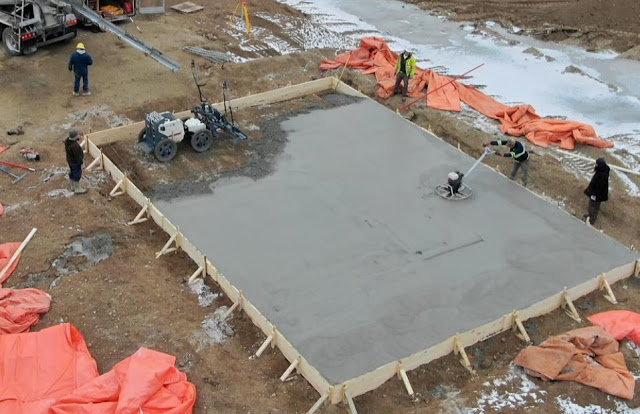 |
Image Credits: Waddell Engineering Ltd |
Floating slabs are constructed to utilize an area as a base foundation for workshops, garages, additional rooms, and sheds. It is mostly employed where there is no need for a standard foundation design.
Here, in this article, let’s discuss the basic features, applications, and advantages of floating slabs in construction.
Concept of Floating Slabs
A floating slab (slab-on-grade), is a type of concrete foundation slab that rests directly on the ground without separate footings, making it suitable for areas with soil challenges like frost heaving or high water tables.
In contrast, a monolithic slab is a single, continuous concrete foundation with integrated footings, typically used in stable soil conditions. The key distinction is that floating slabs rely on the natural bearing capacity of the soil, while monolithic slabs have integrated footings.
The floating slab is a type of slab-on-grade system that was initially developed to mitigate the issue of frost heaving that happens below the building. In freezing regions, a floating slab construction enables the water collected under the building to drain through the pad and move downgrade. This leaves no water under the building to freeze preventing no heaving or uplifting issues for the building.
As floating slabs get support only from the ground underneath the surface, it is not used for large load-bearing construction.
Construction of Floating Slab
Floating slabs are the most affordable foundation one can install for small purposes. They do not require heavy excavation work for footing construction. It simply undergoes three major processes: leveling the ground, constructing the slab mold, and final concrete pouring. Based on the site conditions, a few additional processes may be included.
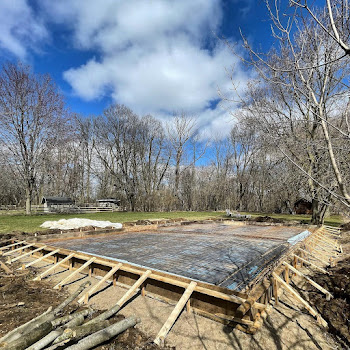 |
Image Credits: Waddell Engineering Ltd
|
Here's a detailed breakdown of the floating slab construction process:
Step 1: Site ExcavationThe initial phase of floating slab construction begins with clearing the land and excavating the designated area according to the construction plan. This essential step serves as the foundation's preparation.
Step 2: Laying Gravel Base for Drainage
Over the excavated area, a layer of gravel is laid. This gravel base not only provides stability but also facilitates drainage, ensuring that unwanted water flows away from the foundation.
Step 3: Reinforcement for Slabs
To enhance the strength and durability of the slab, a slab mold is positioned for the casting process. Reinforcing bars (rebar) are strategically placed within the slab according to specified dimensions and local building codes.
Step 4: Casted Floating Slab
Concrete is poured into the prepared formwork for the slab. Compaction of the concrete is achieved either through manual labor or mechanical vibration, depending on the project's scale and workmanship. Proper compaction is vital to ensure the slab's structural integrity.
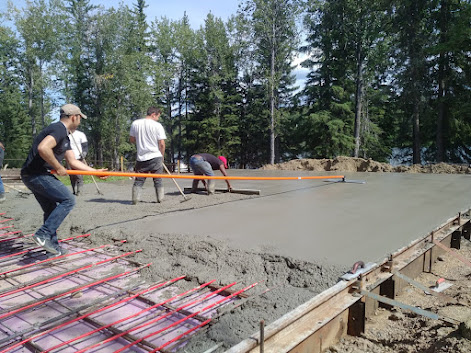 |
Image Credits: Waddell Engineering Ltd |
Step 5: Proper Curing
Following the concrete pouring and compaction, the floating slab requires proper curing, typically for a duration of 2 to 3 days. Adequate curing is crucial to attain the desired strength and durability of the slab.
Advantages of Floating Slabs
- Floating slab construction is cost-effective in areas with low load-carrying capacity, where expensive soil treatment is impractical. It can be used on loose or varying compressibility soil.
- They efficiently distribute vertical loads across a larger area, enhancing stability and preventing concentrated stress points.
- Floating slabs are perfect for house extensions, allowing new construction without impacting existing foundations or structures.
- They act as a moisture barrier, preventing ground moisture from entering the superstructure. This is especially valuable in cold regions, reducing water seepage and frost-related issues. Insulation can be added for further protection.
- Floating slabs eliminate the need for footer trenches, reducing excavation costs.
- Floating slabs do not disrupt the earth layer beneath them, preserving the quality of the underlying soil.
- In regions with shifting soil due to high moisture content, floating slabs are an excellent choice due to their flexibility and adaptability.
Disadvantages of Floating Slabs
- Floating slabs may not be suitable for heavy structures or buildings with significant vertical loads. They are best suited for lightweight structures like garages, sheds, and house extensions.
- In areas with highly unstable or expansive soils that experience significant shifting or settling, floating slabs may be more susceptible to uneven settling and cracking compared to deep foundations with footings.
- While floating slabs can act as moisture barriers, proper drainage, and waterproofing measures must be in place to prevent water infiltration and potential damage to the slab over time.
- In colder climates, additional insulation may be necessary beneath the floating slab to prevent frost-related issues. This can add to the overall construction cost.
- In areas with high water tables, floating slabs may be prone to water-related problems, including hydrostatic pressure and buoyancy issues. Deep foundations with proper drainage may be more appropriate.
- Since floating slabs are typically close to ground level, there may be limited space for utilities like plumbing and electrical systems, potentially requiring adjustments or specialized installation methods.
- Proper site evaluation and soil testing are crucial when considering a floating slab to ensure it is appropriate for the specific soil conditions, which can add complexity and cost to the project.
- Over time, floating slabs may require maintenance, especially if there is settlement or shifting of the underlying soil. Repairs can be more challenging compared to other foundation types.
Read More :
Floor or Slab Systems in Building
0 تعليقات
Commenting Spam Links Are Against Policies