Sand is an important building material that is available in nature that is formed by the decomposition of rocks. It is used as a filler material during the manufacture of mortar or concrete.
Sand is stated as fine aggregates ( size between 4.75 mm and 0.150 mm) in construction. They are mainly composed of small grains of silica (SiO2), which helps to increase the bulkiness or volume of concrete which in turn helps to reduce the overall cost of production. Not just volume, the connected benefits of high strength, high crushing strength, and low shrinkage effects are also achieved by sand in concrete.
No Time to Read?? Watch Video in Our YouTube Channel : Types of Sands Used in Construction
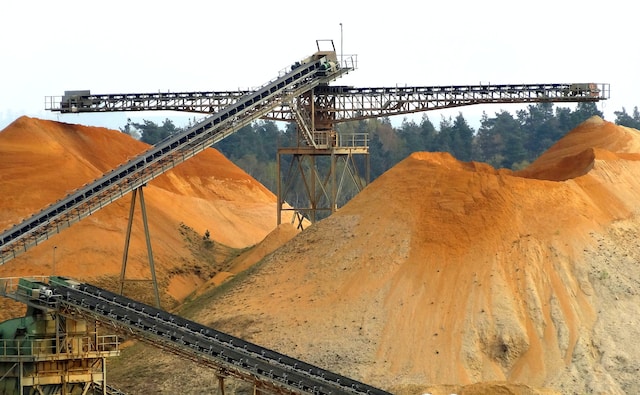
As the construction industry has been consuming sand for decades, the material is facing its way to depletion and hence we humans have come up with new alternative innovative materials for natural sand like Surkhi, quarry dust, etc.
This article is a complete guide about the types of sand in construction, and functions when used in various construction applications.
TABLE OF CONTENTS
- Sources of Sand (Natural & Manmade)
- Classification of Sand
- Properties of Sand
Sources of Sand
The major sources of sand are directly taken from nature. Due to their scarcity, we humans convert other resources in nature or certain by products of construction into artificial sand. Hence, we have natural sources of sand and man-made sources.
Natural Sources of Sand
The natural sources of sand are:
- Pit Sand: Pit sands are sands obtained from pits created 1 to 2m below the ground level. These are usually deposits present underground that contains sharp angular grins and are free from salts. This sand is prepared for construction by removing free clay and other organic materials present in it. Pit sand is mainly used for mortar and concrete construction. Pit sand normally have red-orange color due to the presence of iron oxide in it.
- River Sand: River sand are sand material directly taken from banks or river beds. They are usually obtained in good condition. River sands constitutes fine rounded grains.
- Sea Sand: Sea sand is obtained from sea shores and constitutes fine rounded grains like river sand. As these contain salts, it is avoided for building construction as they attack dampness, efflorescence and disintegration of work.
Man-Made Sources of Sand
- M-Sand or artificial Sand: M-sand, also known as manufactured sand, is a type of sand produced through crushing rocks or aggregates into sand-sized particles. It is a viable alternative to natural river sand in construction and industrial applications. M-sand is made primarily from hard granite, limestone, or basalt rocks that are crushed into sand-sized particles. The crushing process ensures the sand has consistent and angular grains. It is used in concrete production, plastering, bricklaying, asphalt mixes, and tile adhesive.
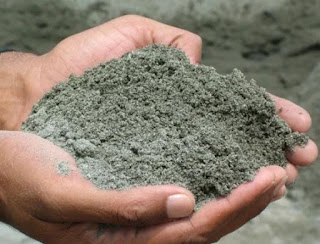 |
M-Sand |
- Concrete Sand: Concrete sand also known as utility sand, pipe sand, manufactured sand, or paver sand is an aggregate sand composed of gneiss, trap rock, limestone or granite. The materials are crushed in quarry , washed and screened for higher quality to avoid large aggregate particles and lay with fine aggregate size range. It is used for pipe laying bed, subgrade for pools, patios, walkways, etc especially for concrete paving types.
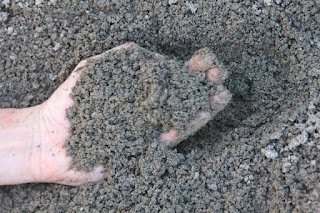 |
Concrete Sand |
- Mason Sand: Mason sand is produced at quarries by crushing granite, gneiss, limestone, or trap rock and then sieving it to remove larger pieces. Finer than concrete sand, it boasts smaller grains, giving it a more aesthetically pleasing appearance akin to beach sand. This visual appeal makes it a popular choice for projects where appearance matters.
Its versatility extends to various applications. Mason sand is commonly mixed with concrete for laying bricks, blocks, and stones. Its fine grain texture makes it particularly suitable for projects such as constructing swimming pools and laying paving stones. Additionally, it finds use in drainage systems, golf course bunkers, and airport runways, showcasing its adaptability across different construction needs.
Classification of Sand
The major classification of sand based on the size of particles are:
- Fine Sand: These are sand passing through a sieve with a clear opening of 1.5875 mm and is commonly used for plastering.
- Coarse Sand: These are sands passing through a sieve with a clear opening of 3.175 mm and are commonly used for masonry work.
- Gravelly Sand: These are sand passing through with a clear opening of 7.62 mm and is commonly used for concrete works.
Functions of Sand in Mortar and Concrete
Sand as a fine aggregate serves the following purpose when used in concrete or mortar:
- Improve strength: Sand helps to adjust the strength of concrete by varying its proportion with the binding material like cement or lime. This hence helps increase the resistance against crushing.
- Improve Bulkiness: Sand in concrete acts as an adulterant. Sand as a fine aggregate along with coarse aggregate constitutes 70 to 80 percent of a the volume of the normal concrete volume. It helps improve the bulk or volume of concrete thereby bringing economy to construction.
- Improve Setting: Sand content provides voids through which access to the atmosphere is possible to improve the hydration of the mass (during setting time).
- Prevent Shrinkae: Sand in concrete helps to fill up the mass avoiding voids after complete setting of the concrete thus preventing drying, cracking, etc.
- Provide Surface Area: The sand particles are fine and hence own large surface area that enable the binding paste to form thin film to adhere and spread facilitating a better hydration reaction.
In conclusion, sand plays a crucial role in construction as a fine aggregate in mortar and concrete. Its properties, including strength, volume increase, and resistance, make it indispensable. However, with its depletion, alternative materials must be considered. Sustainable approaches are vital to meet the ongoing demand for sand and ensure a resilient construction industry.
0 Comments
Commenting Spam Links Are Against Policies