Sulfate-resisting cement (SRC) is a blended cement with the property to resist mineralized water containing sulfates. It is hence used for the construction of underwater structures.
In this blog post, we will delve into the properties, benefits, and applications of sulfate-resisting cement, shedding light on its crucial role in safeguarding concrete against the harmful effects of sulfates.
Table of Contents
- What is Sulfate Resisting Cement (SRC)?
- Working on Sulfate Resisting Cement
- Standard Codes for Sulfate Resisting Cement
What is Sulfate Resisting Cement (SRC)?
Sulfate-resisting cement is used for concrete structures exposed to sulfate-rich environments. Sulfate-resisting cement, also known as SRC, is a specialized type of Portland cement with a material composition that exhibits enhanced resistance to sulfate.
SRC is manufactured by modifying the composition of Ordinary Portland Cement to make it less susceptible to sulfate attack. It has the amount of tricalcium aluminate (C3A) restricted to lower than 5% and (2C 3A +C4AF) lower than 25%, which reduces the formation of sulfate salts.
A stronger relationship exists between the sulfate resistance of concrete and its tricalcium aluminate (C3A) content. The higher the C3A content, the more prone the concrete is to sulfate attack. To improve the sulfate resistance of concrete, lower C3A cement is available. ASTM C 150 Type II cement (MSR) with <8% C3A, and Type V cement (HSR) with <5% C3A are typically specified in sulfate environments.
Check out a general composition of SRC and OPC cement per ASTM standards. It's important to note that the composition ranges provided for both Type V cement and OPC may vary depending on specific manufacturers and regional standards. The percentages mentioned in the table represent typical ranges outlined by ASTM C150.
Table.2. Composition of Type V (SRC) and OPC as per ASTM C150
Composition (%)
|
Type V Cement
|
Ordinary Portland Cement (OPC)
|
Tricalcium Silicate (C3S)
|
35-60%
|
40-70%
|
Dicalcium Silicate (C2S)
|
20-60%
|
15-40%
|
Tricalcium Aluminate (C3A)
|
4-8%
|
5-15%
|
Tetracalcium Aluminoferrite (C4AF)
|
6-20%
|
5-20%
|
Gypsum (added during manufacturing)
|
up to 5%
|
up to 5%
|
The low C3A content minimizes the risk of sulfate-related deterioration, as C3A is highly reactive with sulfates. Let’s understand this concept in a better way.
The following table from ACI 201 recommends the type of cement and w/cm ratio for normal-weight concrete, which will be exposed to sulfates in soil, groundwater, or seawater.
Table.2. Recommendations for the normal-weight concrete subject to sulfate attack
Exposure
|
Water soluble sulfate
(SO4)
in soil,
percent
|
Sulfate (SO4) in water, ppm
|
Cement
|
W/C Ratio Max
|
Mild
|
0.00-0.10
|
0-150
|
---
|
---
|
Moderate
|
0.10-0.20
|
150-1500
|
Type II
IP(MS)
IS(MS)
Type II + Pozzolans
|
0.50
|
Severe
|
0.20
|
1500
|
Type V
Type II + Pozzolan
|
0.45
|
Note
Type IS - Portland blast-furnace slag cement – up to 95% slag permitted; Type IP- Portland-pozzolan cement – up to 40% pozzolan permitted [These are the New ASTM Blended Cement designations as per ASTM C595]
ASTM Performance specification is Type MS – Moderate Sulfate Resistance and Type HS – High Sulfate Resistance.
This partial replacement of Portland cement with a pozzolan such as low calcium fly ash, ground granulated blast furnace slag, or silica fume equally reduces the potential for sulfate attack. These pozzolans consume the calcium in the pore water, reduce the total mass of C3A and decrease the permeability. When deciding which pozzolan to choose, it is important to consider its CaO content.
A high percentage of CaO in fly ash may accelerate the sulfate problem substantially. For instance, ASTM Class F fly ash with <10% CaO will certainly improve the resistance of concrete to sulfate attack. Similarly, silica fume, metakaolin, and natural pozzolans consume Ca to improve sulfate resistance.
Understanding Sulfate Attack - Development of Sulfate Resisting Cement (SRC)
A sulfate attack on concrete occurs when sulfates from external sources, such as groundwater or soil, react with the components of the cement paste in concrete. This reaction can lead to the deterioration of the concrete structure over time.
There are two main forms of sulfate attack, both resulting in the formation of expansive compounds, but involving different reactions.
Reaction 1
The first and most common form of sulfate attack involves the reaction of sulfate ions with calcium hydroxide and tricalcium aluminate hydrates in the cement paste, resulting in the formation of gypsum (CaSO4.2H2O) and extensive ettringite (3CaO.Al2O3.3CaSO4.32H2O or Ca6Al2(OH)12(SO4)3.26H2O).
This reaction occurs under normal temperatures and relatively moist conditions. It begins with the dissolution of calcium hydroxide from the cement paste, leading to an increase in the capillary porosity of the cement paste.
Reaction 2
The second form of sulfate attack in concrete and other cement-based composites results in the formation of thaumasite (CaSiO3.CaCO3.CaSO4.15H2O or Ca3Si(OH)6(CO3)(SO4).12H2O).Thaumasite is a compound that forms during a sulfate attack on concrete. It is a mineral composed of calcium, silicon, carbonates, and sulfates. Thaumasite formation occurs when sulfates react with the calcium silicate hydrates (C-S-H), which are the main strength-giving components of the cement paste in concrete.
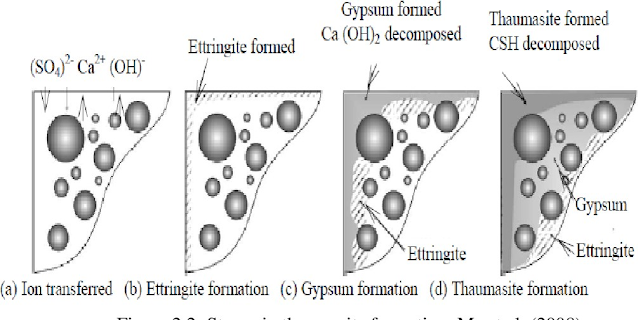 |
Thaumasite Formation in Sulfate Reaction |
Thaumasite can cause significant damage to concrete structures. It forms expansive crystals within the concrete matrix, leading to cracking, loss of strength, and deterioration of the overall structure.
The formation of ettringite or thaumasite products is problematic because it can lead to the expansion and cracking of the concrete, compromising its structural integrity. This is particularly an issue in sulfate-rich environments, such as areas with high sulfate concentrations in the soil or groundwater.
To address this problem, sulfate-resisting cement has been developed. Sulfate-resisting cement is formulated by reducing the tricalcium aluminate (C3A) amount in the cement composition. C3A is the primary component responsible for the formation of ettringite in the presence of sulfates.
Standards for Sulfate Resisting Cement (SRC)
ASTM C150 defines different types of cement based on their composition and performance characteristics. Type V cement is designated explicitly as sulfate-resistant cement. The code ASTM C150 - Type V indicates that the cement meets the requirements for enhanced sulfate resistance.
In Europe, sulfate-resistant cement is typically denoted by the EN 197-1 standard, where sulfate-resistant cement is classified as CEM I or CEM II sulfate-resistant types.
Composition of Sulfate Resisting Cement (SRC)
Sulfate-resistant cement, also known as SRC or Type V cement, is specifically formulated to provide enhanced resistance against sulfate attack. Several factors contribute to its sulfate resistance in terms of composition:
Reduced C3A Content: Sulfate-resistant cement contains a lower percentage of tricalcium aluminate (C3A) compared to ordinary Portland cement (OPC). C3A is highly reactive with sulfates, leading to the formation of expansive compounds that can cause concrete deterioration. By reducing the C3A content, sulfate-resistant cement minimizes the potential for sulfate reactions.
Blended Additives: Sulfate-resistant cement often incorporates blended additives, such as fly ash, silica fume, or slag. These additives help enhance the cement's resistance to sulfates and improve other properties like strength, durability, and workability. They contribute to the formation of a denser concrete matrix, reducing permeability and vulnerability to sulfate penetration.
Limited Gypsum: In the manufacturing process of sulfate-resistant cement, the amount of gypsum (calcium sulfate) is typically minimized or eliminated. Gypsum is commonly added to OPC to control the setting time. However, in sulfate-resistant cement, reducing the gypsum content helps improve its resistance to sulfates.
Fineness: Sulfate-resistant cement is often ground to a higher degree of fineness compared to OPC. Increased fineness provides a larger surface area for chemical reactions and enhances the cement's reactivity, strength development, and resistance to sulfate attacks.
Controlled Mineral Composition: The selection and control of raw materials in sulfate-resistant cement production play a crucial role. The composition is carefully balanced to reduce the presence of minerals that can react with sulfates, ensuring better resistance over the long term.
By combining these factors, sulfate-resistant cement exhibits improved resistance to sulfate attacks and are commonly used in construction projects where the concrete may be exposed to sulfate-rich environments, such as marine structures, wastewater treatment plants, and areas with high sulfate soil or groundwater.
0 تعليقات
Commenting Spam Links Are Against Policies